This month we continue the story of the Concrete Transit Mixer in Australia – this time in the present 2021 setting. From the 1990’s Cesco Australia Ltd (CAL) had been in the business of designing and developing Semi-Trailer Mixer units – from 10m3 to 12m3 capacities. In 2013, CAL in conjunction with development partners BTE (Bulk Transport Equipment), developed the current state-of-the-art 11m3 Semi-Trailer Mixer model, which was delivered to Hanson Concrete in 2014.
The 11.5M3 capacity Big Rig Trailer Mixer bought a new meaning to “big pours” for the likes of Hanson & Hymix nationally, Economix in Victoria & Hallett Transport in South Australia to name a few. The current model incorpo-rated a revolutionary innovation in radio-controlled steering. It was the first rear-axle, “Steerable Trailer” which de-livered a hugely-improved turning circle, making it ideal for access in city areas and tight project-site demands that required larger pours.
In point of fact, it was the sale of an existing 11.m3 Trailer Mixer from Hallett Logistics to McEvoy Transport that started the ball rolling in the development of the Semi-Detachable. The best plans are mostly borne out of opera-tional necessity – and so it was with the Semi-Detachable Trailer Mixer.
Tim McEvoy of McEvoy Transport and EPC Concrete, had an extensive fleet of Prime Movers that had a growing need for something like this Big Rig. Tim’s companies are situated at Ceduna, some 800 kilometers west of Adelaide. Some of his concrete pours therefore can accommodate a 200-kilometer radius. This would then make EPC Concrete one of the remote-pour specialists in the country.
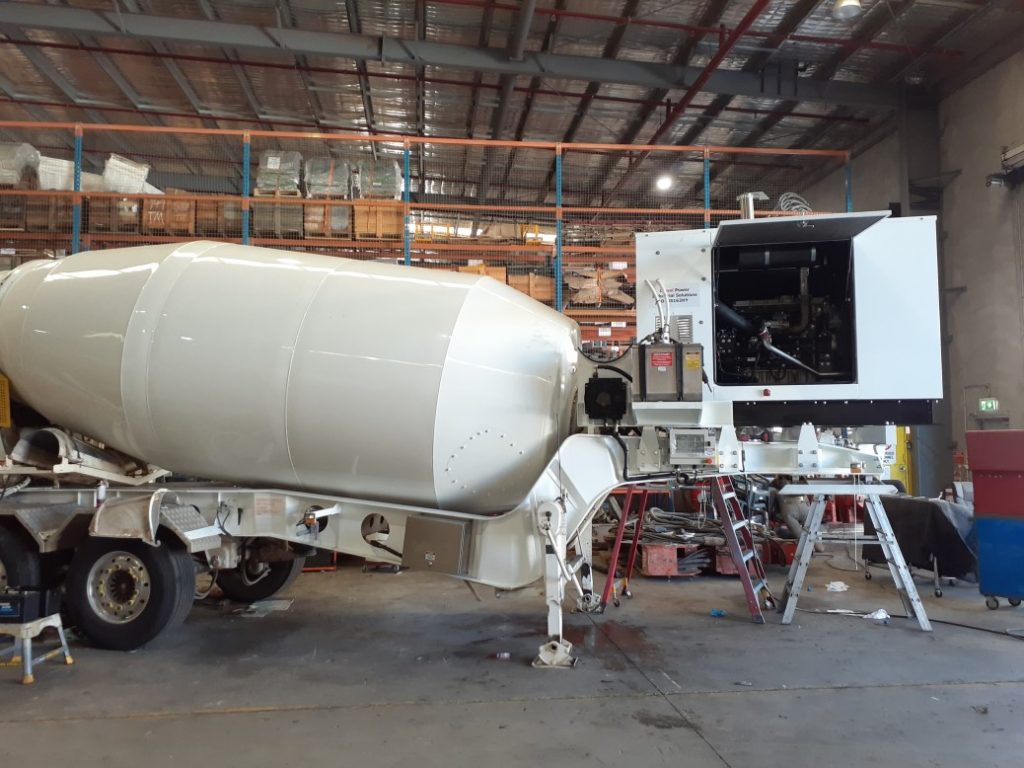
Tim’s plan was to have the capability to interchange the one Trailer Mixer with any of the Prime Movers in his fleet. He had been planning this move to give him the ultimate flexibility of operational responsiveness for some time, as he had a lot of jobs in the 5-10m3 range. EPC are building their own Batch Plant at Ceduna, further increasing the “fit” and applicability of the Semi-Detachable.
The Semi-Detachable presents great advantages over individual, truck-mounted mixers in that you would simply un-hook from one and hook-up with another Prime Mover; depending on the operational need. Future long-distance projects of the companies encompass quite a chunk of South Australia – west 480kms to Border Village on the WA border; another 400kms north to Maralinga Mission and of course east back through the Gawler Ranges and through Port Augusta, down to Adelaide. Tim future plans are to incorporate the Semi-Detachable onto Road Trains.
All drivers within the fleet will be trained on the operation of the Semi-Detachable, thereby ensuring multi-skilling and therefore easy transfer of truck change-overs within the fleet. The only issue that will have to be worked out is a possible vision issue (due to the large Power Pack on the front of the Semi-Detachable). Tim envisages these is-sues to be catered for by a camera array controlled by the Driver, which will enhance better vision and add to safety requirements.
So, all that needed to be done was for Cesco Australia to design and build the Big Bertha unit. Here’s how the project unfolded: –
The team at CAL, comprising our Technical Workshop Guru, Brian Rawlinson (Head Project Manager for this project); along with expert input from our Engineering, Boiler making and Fitting personnel, set out to deliver the all-new Semi-Detachable to the specific requirements of Tim McEvoy of McEvoy Transport. What Brian and his team had to optimize in the re-design of the unit was the importance of it delivering optimal performance capability in all environmental situations – heat, cold, dust, rain, mud etc. as well as catering for an easy-to-use func-tionality for the operator.

Brian and our Engineering team looked at providing the most viable power pack output, combined with weight to performance capability, plus a whole host of other options. One of these important options was the calculation and selection of the required Power Pack to power the big rig. CAL Engineer Mike calculated the size to output the re-quired torque that could comfortably carry and rotate the load.
The calculation for the 11.5m3 at 2.35m3 tonnes per cu. mt. resulted in a power output needed of 125kWs required to rotate the Barrel at 18 rpm. Based on these engineering calculations, CAL MD Gary Webster took into account a planned overload factor to cater for any issues that may arise. The determination was that the Power Pack was to be driven by a Perkins 6-cylinder turbo-charged diesel engine producing 162kW of power and 900Nm of Torque @ 1400 rpm output – the ideal power to output combination to run the Trailer independently, when shackled to a host Prime Mover.
Now getting back to Brian’s team on the construction of the unit. The front carry section of the Trailer Frame had to be designed to accommodate this huge Power Pack. A specific, re-inforced, heavy duty carry case was designed and developed, then welded to the Trailer body. The Power Pack would function as its own control centre with an elec-tronic control panel mounted within the Power Pack body cage, onto the side of the Trailer.
Operation of the Mix/Discharge function would be remotely controlled by interfacing with the Control Panel – mounted on the side of the Trailer and fitted at eye level, utilizing a Woodtech Electronics Control system. The Trailer operator using this control panel can also utilize a remote hand-piece, allowing them to easily move around the Mixer unit directly controlling discharge functions and chute oper-ation.
The Semi-Detachable therefore presents signifi-cant advantages and responsiveness to a fleet operator in that the unit provides an easy-to-use, change-over function; easily transferrable between Prime Movers in a fleet operation. This when combined with a superior power to output combination to run the Trailer as an independent Mixer gives a fleet operator an unmatched, economical solution to undertake big pours easily and proficiently.